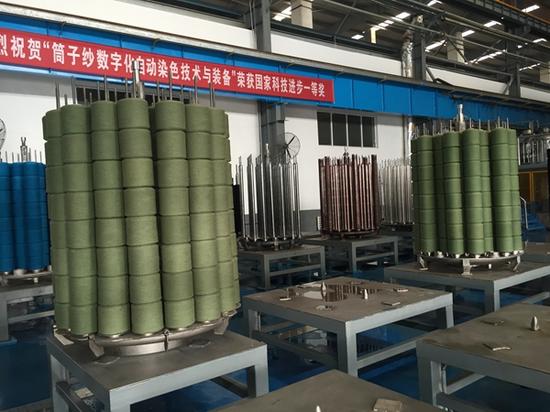

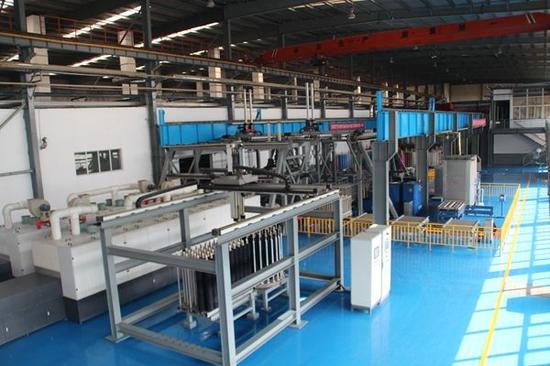
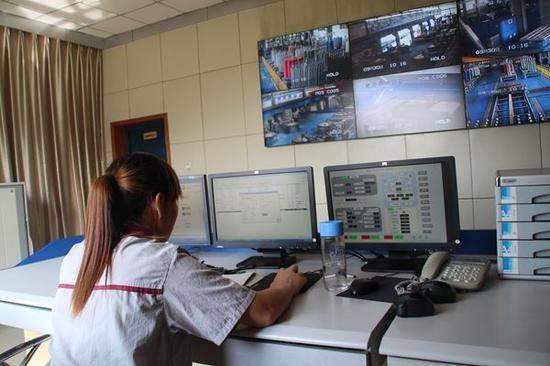
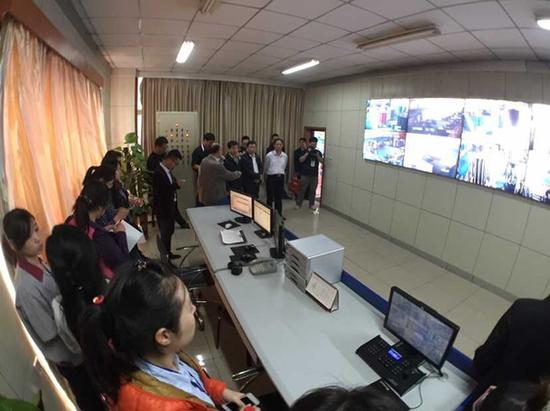
大众网泰安10月16日讯(记者 马俊骥 王洪玲)提起纺织印染,大家首先想到的可能是忙碌的工人、拥挤的车间和横流的污水。今天上午,第十一届中国网络媒体山东行采访团在位于山东泰安的康平纳集团看到的却俨然是一幅智能工厂的模样:整洁的车间里难寻工人踪影,总控室里,电脑控制下的机器手穿行不休,一批批筒子纱就整齐地印染完成。巨大的转变依赖该公司完成的“筒子纱数字化自动染色成套技术与装备”,2014年,该项目获得国家科技进步一等奖,传统产业因科技而转型升级、改头换面。
纺织印染车间大变样,智能工厂里无人化生产
走进位于泰安市的山东康平纳集团的筒子纱染色车间,让人很难想象这里正在从事的是以往“高人工、高污染、高能耗”的纺织印染行业。只见车间二楼的控制室里,工人轻按摁钮,就完成了对整个生产线的控制;控制室外面,整洁明亮的车间里只有两三名工人在巡视设备;工人身边,机械手有节奏地穿行不休,染色完成的筒子纱就被整齐地摆放在架子上。康平纳集团副总经理、总工程师鹿庆福告诉采访团记者,这就是康平纳集团在2014年度国家科学技术进步一等奖项目——筒子纱数字化自动染色示范生产线的基础上升级建立的筒子纱染色智能工厂。
从传统产业到智能工厂,康平纳集团走过了十年艰辛的创新之路。山东康平纳集团有限公司创建于1998年,公司成立之初,只是一家单纯的毛纺企业。2003年,康平纳集团成立五年后,为了打破“永远落后国外先进企业技术一步”的魔咒,开始加强与机械科学研究总院、中国科学院等科研院所的科技合作,走上了科研创新、转型发展之路,目前主营业务升级为高档羊绒面料、染整机械装备及数控机床制造。
“一般来说,行业内做设备的人不完全了解生产工艺,负责生产工艺的人又不懂设备行业实际,使得工艺和设备之间存在滞后性,影响了升级发展。”鹿庆福说,康平纳作为一家面料企业,积累了丰富的染整生产经验,能够从市场的角度分析生产什么样的面料需要什么样的机器,加入机械设备制造业务让这家企业可以说既会“打鱼”又会“造船“。
生产线人工削减80%,项目获国家科技进步一等奖
2009年,康平纳集团创建了国内首条全自动筒子纱染色生产示范线,在之后5年的运行过程中,不断研究完善提升,荣获2014年度国家科学技术进步一等奖,成为我国纺织机械史上第一个国家科技进步一等奖。在筒子纱数字化自动染色示范生产线的基础上进行智能升级,康平纳集团建立了筒子纱染色智能工厂,进一步解决了传统染色车间染色效率低、资源浪费大等问题,实现生产现场无人化,提升了生产效率。“以前一条生产线需要约100名工人,如今只需要20人。“鹿庆福说。
全自动生产线不仅仅大大提高了生产效率,减少了人工成本,而且极大地提高了产品的质量。“产品质量从中档提升到高档,首先要尽可能的消除人为因素对产品的影响,智能工厂就较完美的解决了这一问题。”鹿庆福介绍说,建立智能工厂后,以机器人代替人工操作,可减少一半以上人为因素对产品影响。“比如染化料的配料以克为单位,以前靠工人用天平人工称量,误差不可避免。有了全自动配料系统后,精度可达0.1克,品质可以提升五到十倍。”鹿庆福说。
传统产业因科技而改头换面,每年节省10个西湖的水
不仅如此,全自动智能工厂对节能、环保的贡献也很大。鹿庆福介绍说,以染色环节为例,平常大家所穿的衣服染色需要6个小时,吨纱染色在一般企业的用水量达120—130吨。“也就是说染一吨纱要用一百多吨水来冲洗,而我们现在建设的智能工厂生产线,用水量为80—85吨,节水27%。”鹿庆福给采访团记者简单地算了一笔账:“如果全国整个行业有约1/3到1/4的企业使用这条生产线建成类似智能工厂,每年能够节约10—11个西湖的水。”
依靠科技创新,传统产业实现了转型升级、改头换面。“万众创新,创新并非高不可攀,任何个人和企业都可以成为创新的主体。”康平纳集团总经理刘琳介绍说,“我们集团每年投入的科技活动经费占销售收入的5%以上,科技创新给企业带来收益远大于此。科技是第一生产力,创新给我们带来了源源不断的驱动力。”