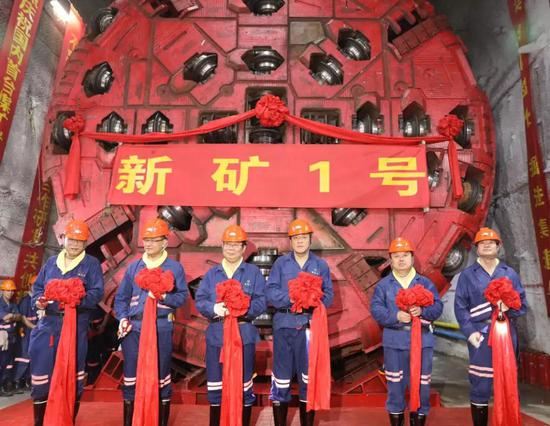
7月20日上午,国内首台煤矿大直径、大埋深、长距离煤矿岩巷全断面盾构机 “新矿1号”,在新巨龙公司顺利始发。
为解决新巨龙公司巷道埋深大、断面大、距离长等诸多施工难题,秉承“跨行越界、为我所用”的原则,集团公司决定引进“新矿1号”TBM盾构机。它集掘进、出渣、支护、除尘、通风、导向、防爆技术于一体,高度机械化、自动化,可有效解决施工过程中粉尘大的难题,大幅提高煤矿岩巷施工效率、降低工人劳动强度、改善作业环境,掘进效率可提升5到10倍。
新巨龙公司总经理李伟介绍,新巨龙公司掘进最初模式用的是靶装机爆破作业,每个月平均进尺30平米断面一般50米,后来升级为奥钢联620综掘机,全岩巷道月进尺最理想状态下90多米、高掘100米,盾构机投用后,设计月进度500米。在人员使用方面,靶装机每个班需要40-50人,奥钢联综掘机需要25-30人,这台盾构机整个操作过程只需8个人。
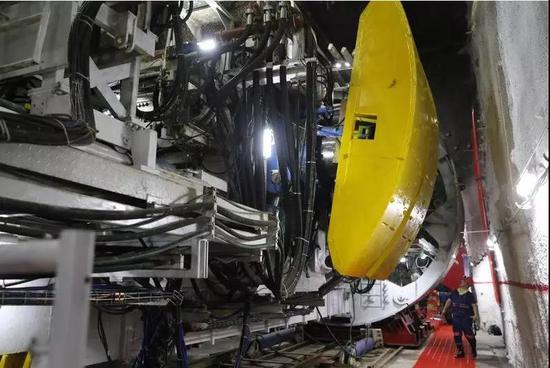
据介绍,整个盾构机下线后被拆解为352件零部件,自4月26日,第一批零件从沈阳抵达新巨龙公司后,他们全力做好到矿验收、地面卸车存放、井下运输及组装等各环节的重点工作。5月9日,伴随着“新矿1号”刀盘中心块从新巨龙公司副井罐笼运达井下,盾构机下井运输工作全面开始。对于这个庞然大物来说,如何从地面运输到井下本身就是一个世界级的难题。

新巨龙公司副总经理周建介绍,前期,为保证盾构机零部件顺利下井,他们提前采用VR技术进行了安装使用模拟实验,更换了副井罐笼,打造了创省内煤矿巷道超高、超大断面之最的盾构机安装硐室,改造运输路线,并进行路线刷扩保障盾构机大件运输,确保高效、快速完成盾构机安装。
经过2年的研究论证,从设计开发到正式下线,从高效组装到始发试车,从最初的炮掘,到综掘,到如今的盾构机,“新矿1号”盾构机始发的一小步,创造了煤炭行业掘进方式的新时代,必将成为中国煤矿建设史上的一大步。在集团公司全力打造“行业内新旧动能转换标杆企业”、加快推进“智慧矿山”建设的大背景下,将会有更多、更安全、更高效、更智能的高科技装备应用到煤矿中来,切实将员工从恶劣的生产环境中、从繁重的体力劳动中解放出来,让煤矿更安全、更智慧,让员工更体面、更幸福。
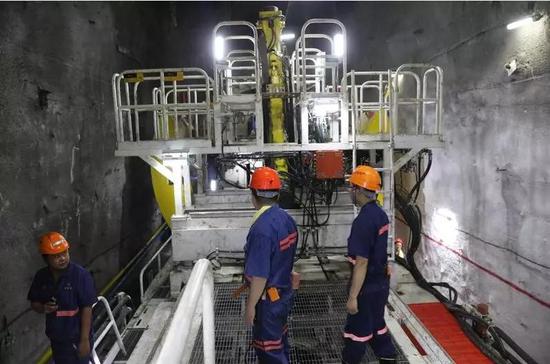
“这是国内首台煤矿大直径、大埋深、长距离岩巷全断面盾构机,它的投用意义非凡,颠覆了整个煤炭行业传统掘进模式,也是新矿推进绿色智慧矿山建设一个质的飞跃,它大大保证了安全,提高了掘进效率,对推进绿色智慧矿山建设将做出不可磨灭的贡献。”集团公司党委常委、副总经理公建祥说。